Spiralbohrer (Wendelbohrer)
- Yurii Kotsun
- 3. März
- 6 Min. Lesezeit
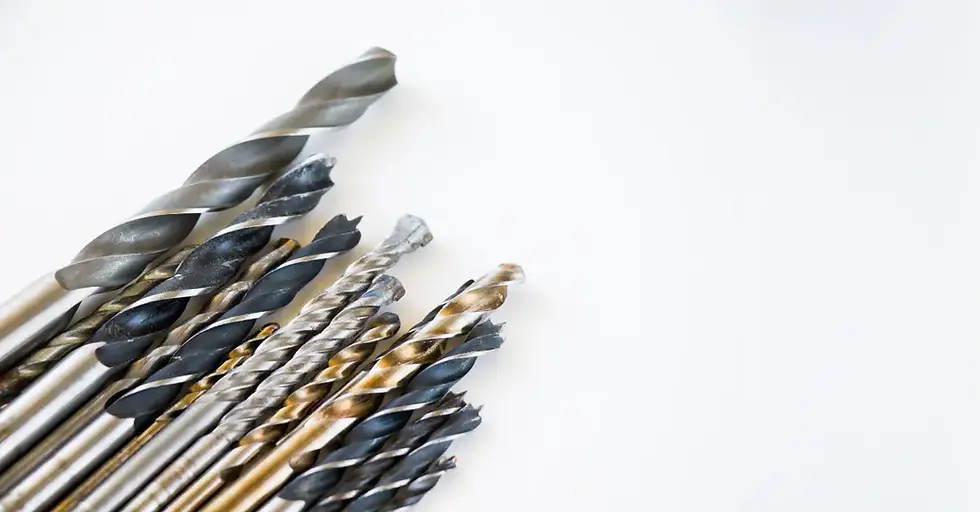
Spiralbohrer, auch Wendelbohrer bekannt, ist ein grundlegendes Werkzeug der Metallbearbeitung und wird hauptsächlich zum Bohren von Bohrungen in verschiedenen Werkstoffen verwendet. Seine Effizienz und Einsatzmöglichkeit werden maßgeblich von seiner Geometrie bestimmt. Die DIN 1412 beschreibt die relevanten Geometrien und ihre Anpassung an unterschiedliche Werkstoffe und Anwendungen.
Ein Spiralbohrer besteht aus mehreren funktionalen Elementen. Die Abbildung 2 zeigt die wichtigste davon.

Bohrerspitze. Der Bereich, der zuerst mit dem Werkstoff in Kontakt kommt und die Hauptschneide enthält. Sie bestimmt wesentlich die Zentrierung und den Materialabtrag.
Spitzenwinkel: Der Winkel an der Bohrerspitze (typischerweise 118° bis 135°) beeinflusst die Schneidleistung und die Zentrierungseigenschaften des Bohrers. Ein größerer Spitzenwinkel eignet sich für harte Werkstoffe, ein kleinerer für weiche Werkstoffe.
Querschneide. Die Linie zwischen den beiden Hauptschneiden. Sie verursacht zusätzliche Reibung und beeinflusst die Schnittkräfte. Ein Kreuzanschliff kann diese Kräfte reduzieren.
Führungsfase. Der Bereich an der Außenseite des Bohrers, der das Bohrloch führt und stabilisiert. Sie reduziert das Verkanten und sorgt für ein sauberes Bohrloch.
Spiralnut. Sie dient der Spanabfuhr und der Zufuhr von Kühlmittel. Ihre Form beeinflusst die Stabilität und die Spantransportkapazität.
Spanwinkel. Dieser Winkel bestimmt die Spanbildung und den Materialabtrag. Er variiert in Abhängigkeit vom Werkstoff und der Bohreranwendung.
Hauptschneide und Nebenschneide. Die Hauptschneide ist für den eigentlichen Materialabtrag verantwortlich. Die Nebenschneide sorgt für die Endbearbeitung und beeinflusst die Dimension sowie die Qualität der Bohrung.
Spiralbohrer können je nach Ausführung und Einsatzzweck unterschiedliche Schneidenanzahlen haben. Die meisten Spiralbohrer sind zweischneidig. Sie verfügen über zwei Hauptschneiden und eine Querschneide. Die zweischneidigen Bohrer bieten eine gute Zerspanungsleistung bei einer Vielzahl von Materialien und sind universell einsetzbar. Sie sind ideal für allgemeine Bohrarbeiten in Werkstoffen wie Stahl, Aluminium, Holz und Kunststoffen und eignen sich besonders gut für präzise Bohrungen in Standardanwendungen.
Dreischneidige Bohrer hingegen besitzen drei Hauptschneiden. Diese bieten eine höhere Stabilität und geringere Vibrationen, was zu gleichmäßigeren und glatteren Bohrungswänden führt. Sie sind ideal für harte und zähe Werkstoffe wie gehärteten Stahl oder Titan. Allerdings erfordern sie mehr Vorschubkraft und sind schwieriger nachzuschärfen.
Mehrschneidige Bohrer mit vier oder mehr Schneiden bieten extreme Stabilität und eine verbesserte Lebensdauer. Diese Bohrer sind speziell für Anwendungen wie die Schwerzerspanung und das Bohren großer Durchmesser konzipiert. Sie eignen sich für abrasive oder schwer zerspanbare Werkstoffe wie Gusseisen oder Edelstahl. Die Herstellung und das Nachschleifen solcher Bohrer sind aufwendiger, und sie werden meist in spezialisierten Maschinen eingesetzt.
Moderne Bohrer können auch mit einer inneren Kühlschmierstoffzufuhr ausgestattet sein. Diese Bohrer verfügen über runde (im Querschnitt) Kühlkanäle, die eine direkte Zufuhr des Kühlschmierstoffs unter Druck in die Bearbeitungszone ermöglichen. Dies fördert die Spanabfuhr erheblich und trägt gleichzeitig dazu bei, die Prozesstemperatur zu senken.
Anschliffformen
Die DIN 1412 klassifiziert verschiedene Anschliffarten, die je nach Werkstoff und Anwendung ausgewählt werden. Die Abbildung 3 gibt eine Übersicht über alle normierten Anschliff-Formen.

Eine zentrale Anschliffart ist der Normalanschliff (Kegelmantelanschliff). Der Normalanschliff ist für alle üblichen Bohrarbeiten in Stahl, Buntmetallen und Kunststoffen geeignet. Die Spitzenwinkel werden an die Zerspanbarkeit der Werkstoffe angepasst. Kräftige Hauptschneiden sind gegen Stöße und Seitenkräfte unempfindlich. Einfache Geometrie sorgt dafür, dass der Bohrer auch von Hand nachgeschliffen werden kann. Die breite Querschneide erfordert aber eine hohe Vorschubkraft (Ff), was bei manchen Anwendungen nachteilig sein kann [1, 2].
Eine weitere wichtige Anschliffart ist die ausgespitzte Querschneide (Form A). Sie wird bevorzugt bei Bohrern mit starkem Kern und großem Durchmesser eingesetzt, besonders beim Bohren ins volle Material. Diese Variante bietet eine gute Zentrierung beim Anbohren durch die Verkürzung der Querschneidenlänge auf etwa 1/10 des Bohrdurchmessers und verringert die erforderliche Vorschubkraft. Allerdings sind zusätzliche Schleifarbeiten erforderlich [1, 2,4].
Die ausgespitzte Querschneide mit korrigierter Hauptschneide (Form B) nach DIN 1412 wird bei Bohrern für Stähle mit hoher Festigkeit, Manganstähle mit über 10 % Mangan, harte Federstähle sowie zum Aufbohren verwendet. Sie zeichnet sich durch ihre Unempfindlichkeit gegen Stöße, einseitige Belastungen und Seitenkräfte aus und verhindert ein Einhaken bei dünnwandigen Werkstücken. Nachteile dieser Variante sind die hohe Vorschubkraft, die Neigung zum Verlaufen und der Mehraufwand beim Nachschleifen [1, 2].
Eine dritte wichtige Variante ist der Kreuzanschliff (Form C). Diese Anschliffart wird bei Bohrern mit sehr starkem Kern eingesetzt und eignet sich besonders für zähe und harte Werkstoffe sowie für Tieflochbohrer. Der Kreuzanschliff sorgt für eine gute Zentrierung und reduziert die erforderliche Vorschubkraft. Durch die Spanteilung wird der Spantransport verbessert. Allerdings ist ein einwandfreier Nachschliff nur maschinell möglich [1, 2, 4].
Die ausgespitzte Querschneide mit facettierten Schneidenecken (Form D) wird bei Bohrungen in Grauguss, Temperguss und Schmiedestücken eingesetzt. Diese Geometrie schont die Schneidecken durch verlängerte Hauptschneiden und ist unempfindlich gegen Stöße. Zudem sorgt sie für eine gute Wärmeableitung, was die Standzeit verbessert. Ein Nachteil ist der Mehraufwand beim Nachschleifen [1, 2, 4].
Die Zentrumspitze (Form E) wird vor allem zum Bohren von Blechen und weichen Werkstoffen sowie für Sacklöcher mit ebenem Grund eingesetzt. Sie bietet eine gute Zentrierung und sorgt für geringe Gratbildung beim Durchbohren. Diese Geometrie eignet sich besonders gut für genaue Bohrungen in dünnen Blechen und Rohren, da kein Einhaken auftritt. Allerdings ist die Zentrumspitze empfindlich gegen Stöße und einseitige Belastungen, und ein einwandfreier Anschliff ist nur maschinell möglich [1, 2].
Der Vierflächenanschliff zeichnet sich durch seine V-Form aus. Diese Geometrie eignet sich besonders gut für das Bohren in kleinen Materialien. Im Unterschied zu anderen Bohrern weist er keinen Kegelmantel auf, sondern ist mit vier flachen Seiten versehen, die ihn für diese speziellen Anwendungen optimal machen. Die vier flachen Seiten bilden eine spitzenartige Querschneide, die eine präzise Zentrierung beim Anbohren ermöglicht.
Der Anschliff der Form U zeichnet sich durch einen ausgespitzten Kern aus, der bis zur Schneidekante mit einer Spanwinkelkorrektur versehen ist. Der positive Spanwinkel erstreckt sich dabei auch über den Kernbereich. Der Bohrer ermöglicht ein leichtes und ruhiges Anbohren, was zu einer konstanten und effizienten Bearbeitung führt. Zudem bietet er hervorragende Spanfördereigenschaften und ist besonders gut für das Bohren großer Tiefen geeignet.
Bohrertypen
Neben den Anschliffarten ist der Seitenspanwinkel ein entscheidender Parameter, der die Spanbildung und die Effizienz des Bohrprozesses beeinflusst. Er beschreibt den Winkel zwischen der Schneidkante und der Tangente an die Spiralnut. Je nach Werkstoff und Anwendung wird zwischen drei Haupttypen von Spanwinkeln unterscheidet: Typ N, Typ H und Typ W. Die Abbildung 4 veranschaulicht die geometrischen Unterschiede der verschiedenen Spanwinkeltypen. Die Spanabfuhr beim Bohrer hängt in hohem Maße vom Seitenspanwinkel ab. Ein größerer Seitenspanwinkel fördert in der Regel eine bessere Spanabführung, da der Span in einem steileren Winkel abführt und weniger Widerstand erzeugt wird.

Typ N verfügt über eine Normalspirale mit einem Seitenspanwinkel im Bereich von 20 bis 30 Grad und wurde für Werkstoffe mit einer Festigkeit von bis 1300 N/mm² konzipiert. Dieser Anschliff eignet sich für unlegierten (C10 – C45, Ck10 – Ck35, 25CrMo5, 20Mn5 usw.), legierten (36CrNiMo4) und hitzebeständigen (X210Cr12) Stahl, rostfreien (X10Cr13) Stahl, Gusseisen (Grauguss, Temperguss). Ebenso ist er für NE-Metalle wie Zink, Aluminium (Al-Legierungen), Leichtmetalle, Messing (CuZn 37, Ms60) und Kupfer geeignet [3].
Die langgedrallte Spirale Typ H weist in der Regel einen Neigungswinkel der Spiralnut von 10 bis 19 Grad auf und wurde für spröde sowie harte Werkstoffe mit einer Festigkeit von 1300 N/mm² und mehr entwickelt. Solche Bohrer werden überwiegend für die Bearbeitung von weichen Kunststoffen (Thermoplasten), Magnesiumlegierungen (z.B. MgAl6Zn3) Hartgewebe und Hartpapier eingesetzt. Sie sind auch für Materialien wie Ultramid, Polyamid, Mn-Stähle und sprödes Messing (Ms58) geeignet [3].
Der kurzgedrallte Spiralbohrer Typ W zeichnet sich durch einen Drallwinkel von 30 bis 40 Grad aus und ist für weiche Werkstoffe wie Aluminium und dessen Legierungen (bis 10% Si-legiert), Kupfer unlegiert sowie zähe und ausgehärtete Leichtmetalle geeignet. Ein wichtiges Merkmal dieses Aufbaus ist der relativ große Spitzenwinkel von bis zu 140 Grad, der in Kombination mit dem Seitenspanwinkel die Schneidkante vergrößert und somit eine verbesserte Schneidleistung ermöglicht [3].
Spiralbohrer sind ein unverzichtbares Werkzeug in der modernen Fertigung. Durch ihre Vielseitigkeit und Anpassungsfähigkeit an verschiedene Werkstoffe bieten sie optimale Lösungen für präzises und effizientes Bohren. Mit verschiedenen Geometrien und Ausführungen bieten sie für jede Anwendung die passende Lösung. Ihre kontinuierliche Weiterentwicklung in Bezug auf Materialeigenschaften und innovative Technologien wie die Kühlschmierstoffzufuhr sorgt für eine höhere Effizienz, längere Standzeiten und eine verbesserte Bearbeitungsqualität.
Quellen:
[1] Fritz Klocke. Fertigungsverfahren 1. Zerspanung mit geometrisch bestimmter Schneide, 2017 (S. 568-579)
[2] Webseite: ruko.de
[3] Jochen Dietrich. Praxis der Zerspantechnik. Verfahren, Werkzeuge, Berechnung, 2016 (S. 146-154)
[4] Berend Denkena, Hans Kurt Tönshoff. Spanen. Grundlagen 2010 (S. 9-14)